Sponsored article
How does the automatic welding process work?
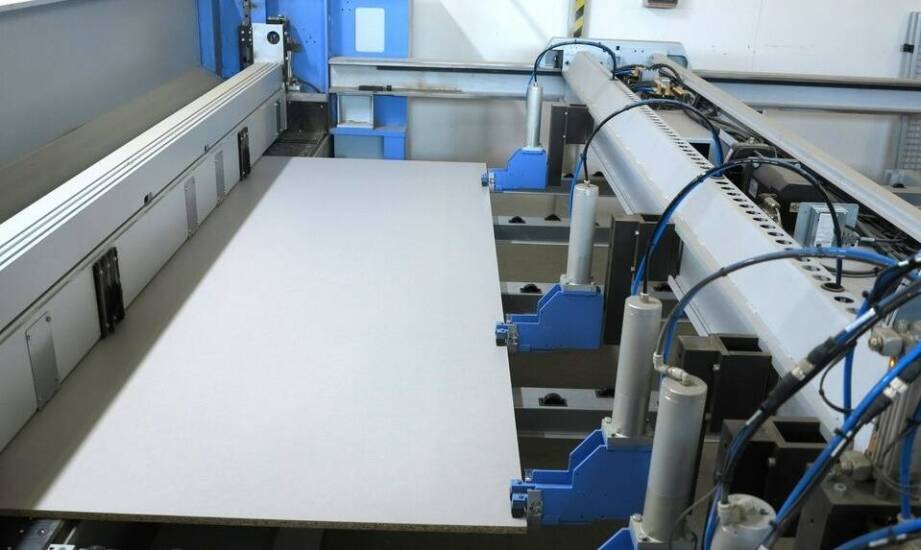
The welding of plastics is a key process in many industries where fast, precise and consistent production of thermoplastic components is required. It involves joining two or more parts by applying heat and pressure, which causes them to melt and fuse together. Automating this process allows for increased efficiency and reduced errors due to manual handling.
Material preparation and parameter setting
The first step is the proper preparation of the material and the setting of the welding parameters. The operator has to choose the right temperature, welding time and pressure, adapted to the specific material and the required strength of the joint. In modern solutions such as PULSA SUPRIM, parameters are precisely controlled by PLC systems, ensuring consistency and high weld quality.
Welding process
Once the material has been prepared, the actual welding process begins. Depending on the applied technology, this may be done using impulse welding, among other methods. The PULSA SUPRIM is an example of a state-of-the-art device using this technology for the precise joining of technical fabrics. The process involves passing an electric current through a resistance tape, which causes it to heat up temporarily. As a result, the material melts at the joining point and then forms a durable, strong joint under pressure.
An automatic welder allows precise control of the heating time and temperature, minimising the risk of overheating and damaging the material. This makes it possible to achieve aesthetically pleasing, strong and uniform joints, which is particularly important in industries requiring a high-quality finish.
Cooling and quality control
Once the welding process is complete, the components must be cooled down to obtain their full mechanical strength. With the impulse welding technology used in PULSA SUPRIM cooling takes place under constant pressure, which excludes the risk of deformation. This ensures that the joints are even and aesthetically pleasing and that the material retains its functional properties.
Quality control of the joint includes both visual inspection and performance tests. Modern systems for monitoring process parameters allow real-time detection of possible deviations, ensuring high repeatability and reliability of welds.
Machines offered by Zemat Technology Group are state-of-the-art solutions that ensure automation of the welding process, high precision and durability of the joints. The use of advanced operating and control systems allows for the best results in a wide range of industrial applications.